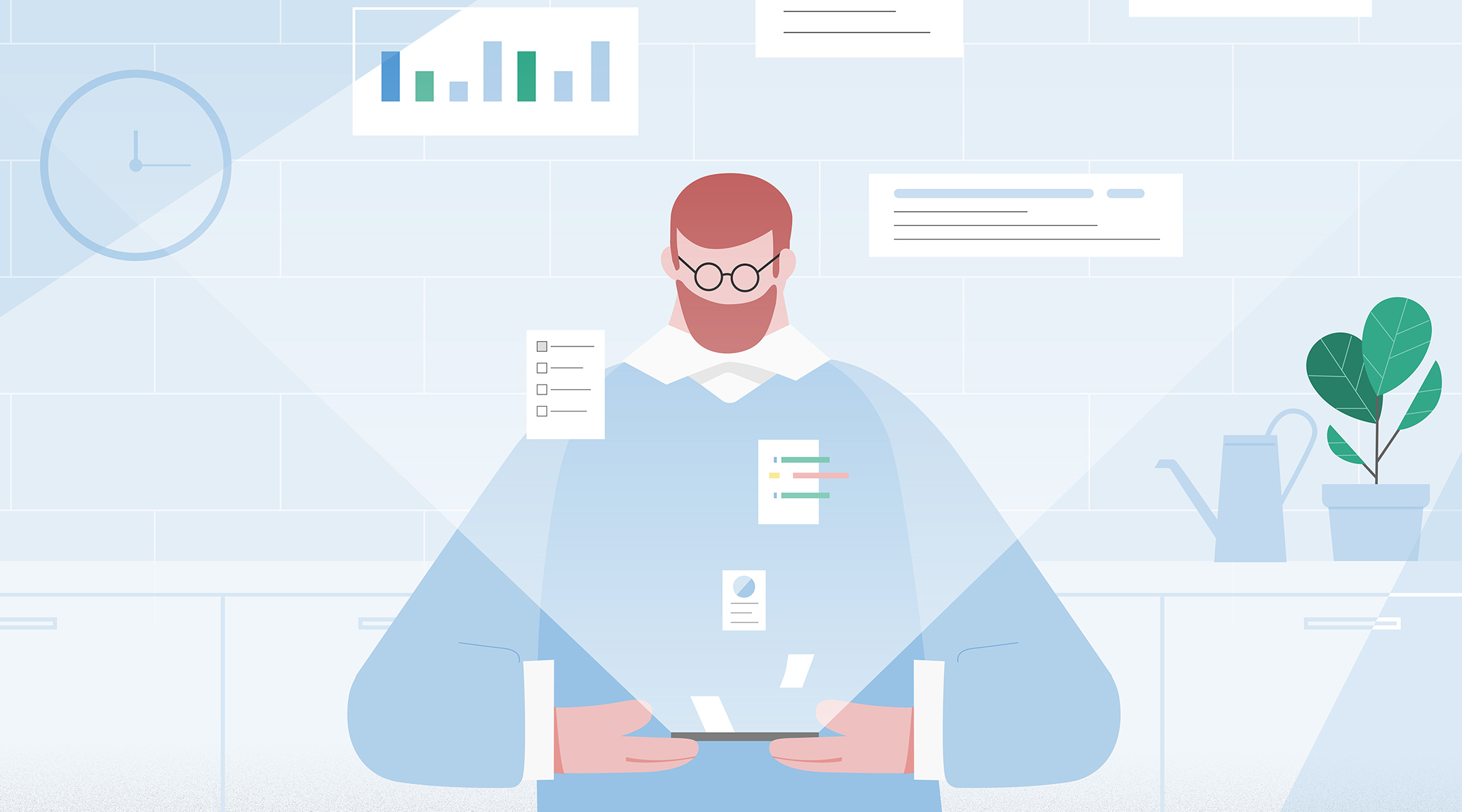
What this guide covers:
Integrating your Critical Business Systems
I know I don’t need to tell you that purchasing a new maintenance software system is a huge and difficult decision. There are pages and pages of solutions out there from fleet maintenance management, GPS, telematics, accounting, ERP, CMMS and EAM. It can be difficult to understand which tools are mission critical, and which may just add to the noise. If your organization utilizes ERP and/or dispatch software and you are assessing whether a fleet maintenance software integration is necessary, this article is for you. Eventually, many ERP users make the decision to fully integrate their dispatch and accounting software with a maintenance platform in order to expand functionality to also automate the shop floor and maintenance departments. Here are 8 reasons to consider an ERP/Maintenance software integration.
1. Synchronize your Accounting Department and Shop Floor
Integrating your accounting software system with a maintenance software system helps to synchronize your accounting team and automatically link them up to the work being done on your shop floor. When parts are used out of inventory on a work order, the journal entries will automatically be booked to relieve that inventory value and expense the correct maintenance accounts. As you are purchasing parts or services from vendors the necessary accounts payable vouchers can be created in most ERP systems. Creating this flow of data across the maintenance and accounting system creates better alignment between departments.
2. Increase Visibility into Maintenance Costs
While accounting system can report on costs related the maintenance process, without an integration into a fleet maintenance software system, you cannot drill down to specific maintenance costs such as work order cost, work order parts usage, parts purchased, inventory count, core tracking, invoicing for owner operators and other 3rd parties, as well as outside services costing. Without visibility into these maintenance costs, organizations cannot create costing reports and capture optimal business intelligence insights.
3. Automate Maintenance for Real-time Results
The maintenance integration allows you to track parts being used on repairs. Without this integration, there is no work order management system tracking the work being done, parts being used, or the value and cost associated to a given repair.
By integrating the software systems, your team can capture and track maintenance in real-time and mitigate the need for double-data entry. Without a maintenance system, someone has to capture and write down information related to maintenance such as inventory count, suppliers, parts used, etc. When they are done tracking that on paper or in Excel, they have to re-enter it into the ERP system. A manual process adds more time and risk to your workflow and increases the amount of manual labour, decreases the timeliness of information, and doubles the risk of typing error.
4. Notify the Dispatch System Regarding Asset Downtime
When an asset repair has begun, the maintenance system can notify the dispatch system. When this occurs, the asset is marked as an unavailable for the duration of its downtime and the dispatch system will be notified again when the asset is ready to be used. A maintenance integration automates the process of pushing updates related to the asset’s repair status. Instead of manually informing relevant parties, dispatchers can be immediately updated when work is complete on the floor. Allowing the dispatch team to plan and become more proactive.
5. Automate the Flow of Data to Quickly Set up New Assets
When new assets are acquired, your team can seamlessly create a stream of data between software systems by adding the assets to the maintenance product and pushing it into the ERP system. You can ensure each system knows about the new asset without additional manual entry and manual labor. Plus, immediately update the dispatch when a new asset is available, improving their responsiveness when a new asset is added to your fleet.
6. Gain Visibility into Mileage with a Meter Integration
Dispatch software helps you seamlessly manage and dispatch assets. Your system likely knows where a particular asset is located at any given time, and how many Miles or KMs it has traveled. Capturing an asset’s precise mileage is critical when it comes to accurately and efficiently managing the preventive maintenance and warranty opportunities on your assets. The maintenance product should be tracking all your preventive maintenance schedules and identifying when there are warranty opportunities for any repairs in process. The only way to be 100% accurate is to push mileage information from your assets into to your maintenance system.
On the flip side, the maintenance software will forecast and track preventive maintenance that is upcoming. Accurate and timely preventive maintenance information benefits the dispatch system as it allows dispatchers to plan around future planned outages, future planned maintenance schedules, or asset downtime.
Dispatch software should put dispatchers is in constant contact with drivers through onboard computers. Those computers can also be used to allow the driver to report an issue with the asset. With a maintenance system / dispatch integration, a reported issue or inspection failure can be communicated right back to the maintenance system for follow-up by a mechanic. The driver reported issues are instantly transmitted to the maintenance team to let them know in real-time if there is an issue with the asset. From here, your team can track the issue resolution including the how, when, and who.
7. Improve Safety and Compliance
Instead of relying on logbooks in a truck, where important data is written down without any advanced visibility into it, an integration with maintenance software allows you to push driver-reported issues directly to the maintenance team to notify them early and often about issues related to safety and compliance.